Zweck von Beschichtungsmaterialien
Die Beschichtung der Außenfläche von Stahlrohren ist entscheidend, um Rostbildung zu verhindern. Rost auf der Oberfläche von Stahlrohren kann deren Funktionalität, Qualität und Optik erheblich beeinträchtigen. Daher hat der Beschichtungsprozess einen erheblichen Einfluss auf die Gesamtqualität von Stahlrohrprodukten.
-
Anforderungen an Beschichtungsmaterialien
Gemäß den Standards des American Petroleum Institute sollten Stahlrohre mindestens drei Monate lang korrosionsbeständig sein. Die Nachfrage nach längeren Rostschutzzeiten ist jedoch gestiegen. Viele Anwender fordern eine Beständigkeit von drei bis sechs Monaten bei Außenlagerung. Neben der Langlebigkeit erwarten Anwender von Beschichtungen eine glatte Oberfläche und eine gleichmäßige Verteilung der Korrosionsschutzmittel ohne Lücken oder Tropfen, die die optische Qualität beeinträchtigen könnten.
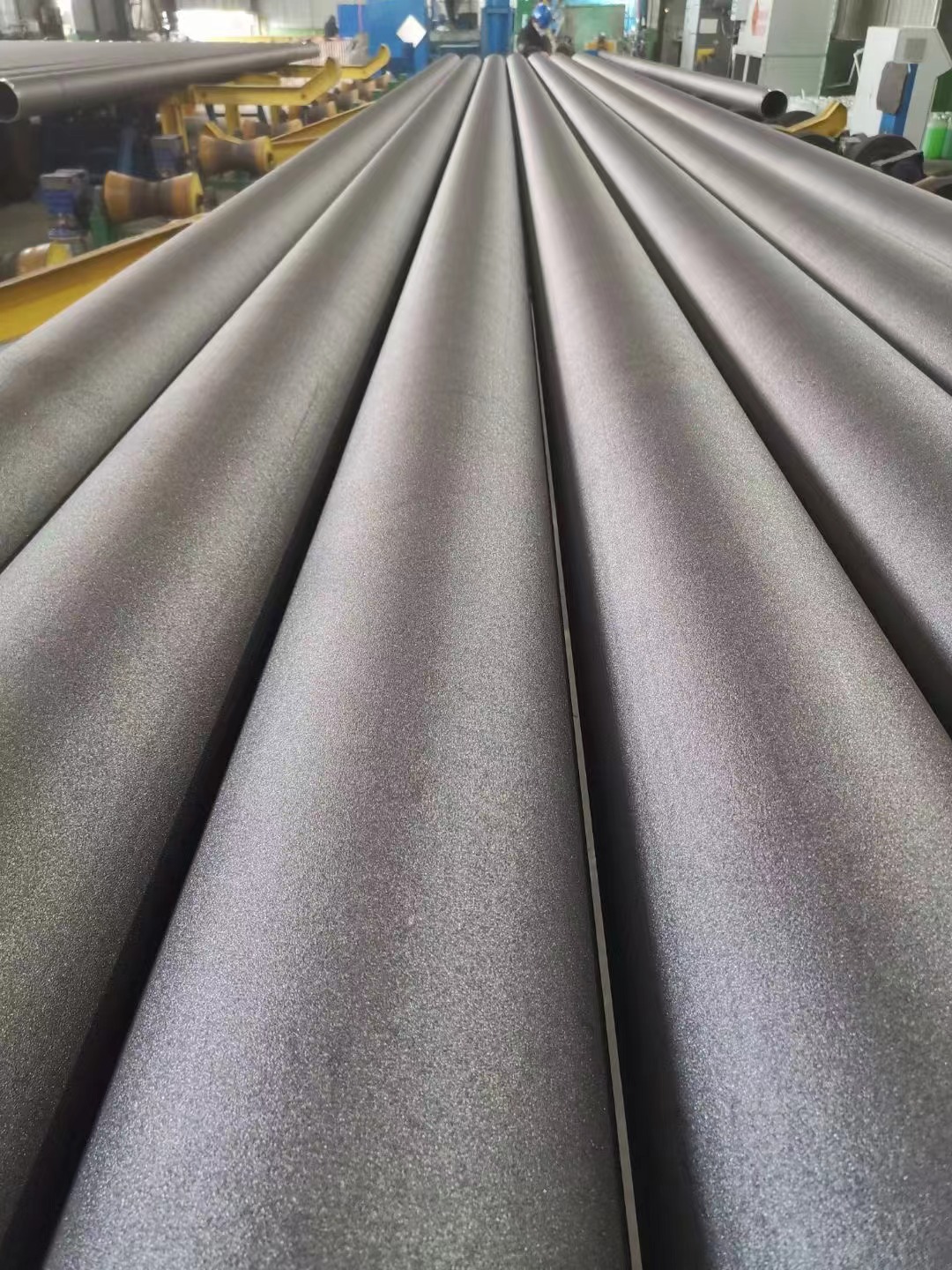
-
Arten von Beschichtungsmaterialien und ihre Vor- und Nachteile
In städtischen unterirdischen RohrnetzenStahlrohrewerden zunehmend für den Transport von Gas, Öl, Wasser und anderen Medien eingesetzt. Die Beschichtungen dieser Rohre haben sich von traditionellen Asphaltmaterialien zu Polyethylenharzen und Epoxidharzen entwickelt. Die Verwendung von Polyethylenharzbeschichtungen begann in den 1980er Jahren, und mit den unterschiedlichen Anwendungen wurden die Komponenten und Beschichtungsverfahren schrittweise verbessert.
3.1 Asphaltbeschichtung auf Erdölbasis
Die Petroleum-Asphaltbeschichtung, eine traditionelle Korrosionsschutzschicht, besteht aus mit Glasfasergewebe verstärkten Petroleum-Asphaltschichten und einer äußeren Schutzfolie aus Polyvinylchlorid. Sie bietet hervorragende Wasserdichtigkeit, gute Haftung auf verschiedenen Oberflächen und ist kostengünstig. Sie hat jedoch auch Nachteile: Sie ist anfällig für Temperaturschwankungen, versprödet bei niedrigen Temperaturen und neigt zu Alterung und Rissbildung, insbesondere in felsigen Böden. Dies erfordert zusätzliche Schutzmaßnahmen und erhöht die Kosten.
3.2 Steinkohlenteer-Epoxidbeschichtung
Steinkohlenteer-Epoxidharz, hergestellt aus Epoxidharz und Steinkohlenteerasphalt, weist eine ausgezeichnete Wasser- und Chemikalienbeständigkeit, Korrosionsbeständigkeit, gute Haftung, mechanische Festigkeit und Isoliereigenschaften auf. Allerdings benötigt es nach dem Auftragen eine längere Aushärtezeit und ist daher während dieser Zeit anfällig für Witterungseinflüsse. Zudem erfordern die verschiedenen Bestandteile dieses Beschichtungssystems eine spezielle Lagerung, was die Kosten erhöht.
3.3 Epoxid-Pulverbeschichtung
Die in den 1960er Jahren eingeführte Epoxidpulverbeschichtung basiert auf dem elektrostatischen Aufsprühen von Pulver auf vorbehandelte und vorgewärmte Rohroberflächen, wodurch eine dichte Korrosionsschutzschicht entsteht. Zu den Vorteilen zählen ein breiter Temperaturbereich (-60 °C bis 100 °C), starke Haftung, gute Beständigkeit gegen kathodische Ablösung, Stoßfestigkeit, Flexibilität und Schweißnahtschäden. Die dünnere Beschichtung macht die Beschichtung jedoch anfällig für Beschädigungen und erfordert anspruchsvolle Produktionstechniken und -geräte, was die Anwendung vor Ort erschwert. Obwohl die Beschichtung in vielerlei Hinsicht hervorragend ist, bleibt sie im Vergleich zu Polyethylen hinsichtlich Hitzebeständigkeit und Korrosionsschutz insgesamt hinter den Erwartungen zurück.
3.4 Korrosionsschutzbeschichtung aus Polyethylen
Polyethylen bietet hervorragende Schlagzähigkeit und hohe Härte sowie einen breiten Temperaturbereich. Aufgrund seiner überlegenen Flexibilität und Schlagzähigkeit, insbesondere bei niedrigen Temperaturen, wird es in kalten Regionen wie Russland und Westeuropa häufig für Pipelines verwendet. Die Anwendung an Rohren mit großem Durchmesser ist jedoch weiterhin problematisch, da dort Spannungsrisse auftreten können und eindringendes Wasser zu Korrosion unter der Beschichtung führen kann. Dies erfordert weitere Forschung und Verbesserungen bei Material und Anwendungstechniken.
3.5 Schwere Korrosionsschutzbeschichtung
Schwere Korrosionsschutzbeschichtungen bieten im Vergleich zu Standardbeschichtungen eine deutlich verbesserte Korrosionsbeständigkeit. Sie sind selbst unter rauen Bedingungen langfristig wirksam und haben eine Lebensdauer von über 10 bis 15 Jahren in chemischen, maritimen und lösungsmittelhaltigen Umgebungen sowie über 5 Jahren in sauren, alkalischen oder salzhaltigen Umgebungen. Diese Beschichtungen haben typischerweise Trockenfilmdicken von 200 μm bis 2000 μm und gewährleisten so hervorragenden Schutz und Langlebigkeit. Sie werden häufig in Schiffskonstruktionen, chemischen Anlagen, Lagertanks und Pipelines eingesetzt.
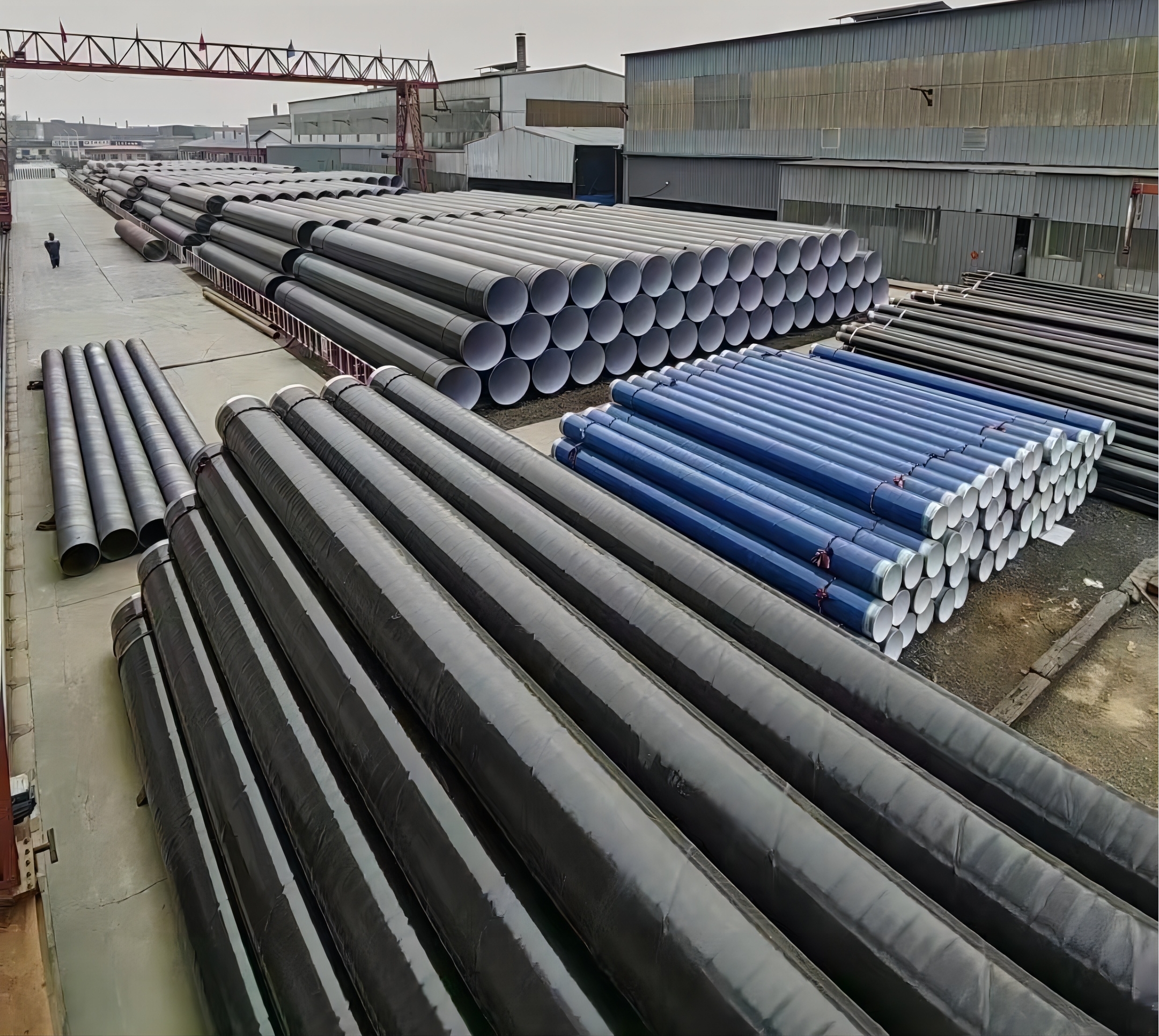
-
Häufige Probleme mit Beschichtungsmaterialien
Zu den häufigsten Problemen bei Beschichtungen zählen ungleichmäßiges Auftragen, Tropfen von Korrosionsschutzmitteln und Blasenbildung.
(1) Ungleichmäßige Beschichtung: Eine ungleichmäßige Verteilung der Korrosionsschutzmittel auf der Rohroberfläche führt zu Bereichen mit übermäßiger Beschichtungsdicke und damit zu Ausschuss, während dünne oder unbeschichtete Bereiche die Korrosionsbeständigkeit des Rohrs verringern.
(2) Tropfen von Korrosionsschutzmitteln: Dieses Phänomen, bei dem sich Korrosionsschutzmittel in Form von Tropfen auf der Rohroberfläche verfestigen, beeinträchtigt die Ästhetik, hat jedoch keinen direkten Einfluss auf die Korrosionsbeständigkeit.
(3) Blasenbildung: Während der Anwendung im Korrosionsschutzmittel eingeschlossene Luft erzeugt Blasen auf der Rohroberfläche, die sowohl das Aussehen als auch die Wirksamkeit der Beschichtung beeinträchtigen.
-
Analyse von Problemen mit der Beschichtungsqualität
Jedes Problem hat verschiedene Ursachen und wird durch verschiedene Faktoren verursacht. Ein durch die Qualität des Problems hervorgehobenes Stahlrohrbündel kann auch eine Kombination mehrerer Ursachen sein. Die Ursachen für eine ungleichmäßige Beschichtung lassen sich grob in zwei Arten unterteilen: Zum einen das ungleichmäßige Phänomen, das durch das Sprühen entsteht, nachdem das Stahlrohr in die Beschichtungsbox gelangt ist; zum anderen das ungleichmäßige Phänomen, das durch Nichtsprühen entsteht.
Der Grund für das erste Phänomen ist offensichtlich leicht zu erkennen: Die Beschichtungsanlage wird mit insgesamt sechs Pistolen (die Mantelleitung hat 12 Pistolen) besprüht, wenn das Stahlrohr in einer 360°-Umlaufbewegung in die Beschichtungsbox gelangt. Wenn die Sprühmenge jeder Pistole unterschiedlich ist, führt dies zu einer ungleichmäßigen Verteilung des Korrosionsschutzmittels auf den verschiedenen Oberflächen des Stahlrohrs.
Der zweite Grund ist, dass es neben dem Sprühfaktor noch andere Gründe für die ungleichmäßige Beschichtung gibt. Es gibt viele Faktoren, wie z. B. Rost an Stahlrohren und Rauheit, die eine gleichmäßige Verteilung der Beschichtung erschweren. Auf der Oberfläche von Stahlrohren bleibt beim Kontakt mit der Emulsion ein Wasserdruck zurück, der die Beschichtung beeinträchtigt. Dadurch kann das Konservierungsmittel nur schwer an der Oberfläche des Stahlrohrs haften bleiben, sodass die Emulsion die Stahlrohrteile nicht bedeckt und die Beschichtung des gesamten Stahlrohrs ungleichmäßig ist.
(1) Ursachen für hängende Tropfen des Korrosionsschutzmittels. Stahlrohre haben einen runden Querschnitt. Jedes Mal, wenn Korrosionsschutzmittel auf die Oberfläche gesprüht wird, fließt das Korrosionsschutzmittel im oberen Bereich und am Rand aufgrund der Schwerkraft nach unten, wodurch hängende Tropfen entstehen. Die Beschichtungsproduktionslinie der Stahlrohrfabrik verfügt über Ofenanlagen, die das aufgesprühte Korrosionsschutzmittel rechtzeitig erhitzen und verfestigen können, wodurch dessen Fließfähigkeit verringert wird. Wenn jedoch die Viskosität des Korrosionsschutzmittels zu niedrig ist, nach dem Sprühen nicht rechtzeitig erhitzt wird, die Heiztemperatur zu niedrig ist oder die Düse nicht einwandfrei funktioniert, kann es zu hängenden Tropfen kommen.
(2) Ursachen für Korrosionsschutzschaumbildung. Aufgrund der Luftfeuchtigkeit am Einsatzort verteilt sich die Farbe zu stark. Ein Temperaturabfall während des Dispersionsprozesses führt zur Blasenbildung im Konservierungsmittel. In einer Umgebung mit niedriger Luftfeuchtigkeit und niedrigen Temperaturen zerstäuben die Konservierungsmittel feinste Tröpfchen, was zu einem Temperaturabfall führt. Das Wasser in der feuchteren Luft kondensiert nach dem Temperaturabfall zu feinen, mit dem Konservierungsmittel vermischten Wassertröpfchen und dringt schließlich in die Beschichtung ein, was zur Blasenbildung führt.
Veröffentlichungszeit: 15. Dezember 2023